Der hessische Büromöbelhersteller König + Neurath hat nach 15 Monaten Bauzeit ein autonomes Hochregallager am Produktionsstandort Karben bei Frankfurt in Betrieb genommen. Die Anlage ist eine der modernsten dieser Art in Europa.
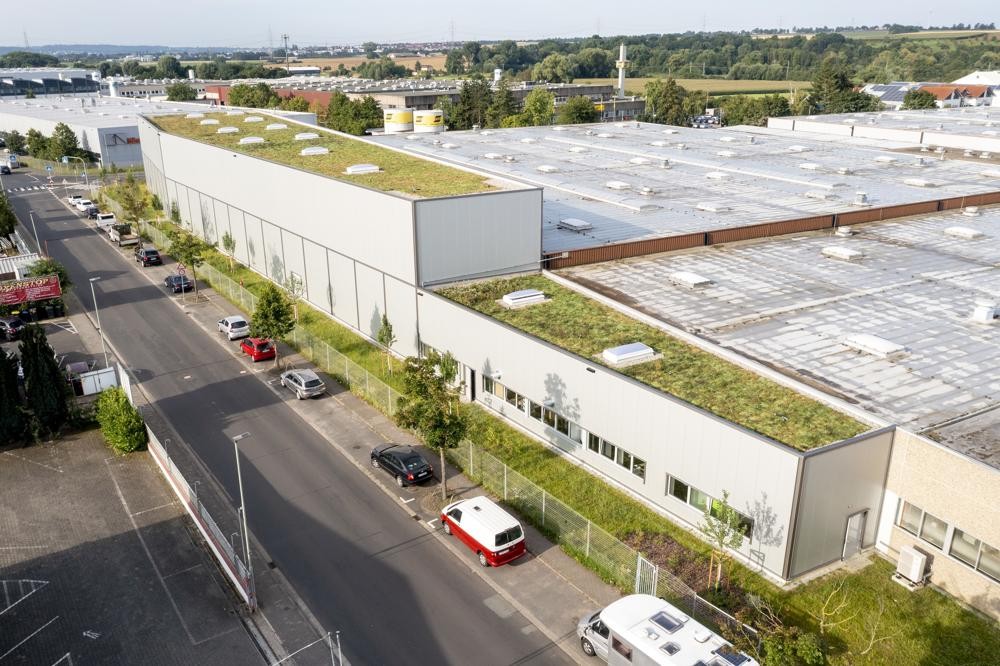
Der Neubau des Lagers war eines der letzten Projekte, die Egon König initiiert und das seine Frau Gerti König mit Engagement nach seinem Tode vorangetrieben hat. Beiden war es wichtig, dem Unternehmen sowie den Kunden und Projektpartnern Bestandssicherheit zu gewährleisten – und die Zukunftsfähigkeit des hessischen Herstellers von Büromobiliar und Raumsystemen zu sichern.
Technik und Größe des Gebäudes beeindrucken
„Im Neubau mit seinen zwölf Metern Höhe, einer Länge von 130 und einer Breite von 20 Metern können ab sofort circa 5.000 Paletten gelagert werden. Wir sind stolz, dass wir diese Kapazitäten jetzt nach nur einem Jahr Bauzeit nutzen können“, freut sich David Schuch, der das Projekt vom ersten Planungsschritt im Jahr 2017 bis zur Fertigstellung betreut hat. „Außergewöhnlich ist nicht nur die beeindruckende Größe des Gebäudes, sondern vor allem auch die Technik, die hier zum Einsatz kommt.“ Das Gesamtkonzept wurde anhand eines „digitalen Zwillings“ entwickelt und umgesetzt. „Der digitale Zwilling wird auch weiterhin genutzt, um die Ist-Prozesse zu analysieren und das System weiter zu entwickeln“, ergänzt Dirk Fischer, Vorstand Produktion/Technik/Einkauf.
„Das Zusammenspiel zwischen mehreren autonom fahrenden Systemen und der Datentechnik ist einzigartig,“ sagt Schuch. Was er damit meint, wird deutlich, wenn man die voll automatisierten Vorgänge live erlebt: Es geht erstaunlich ruhig und geordnet, wenn die autonom fahrenden Hochhubwagen und Schmalgangstapler zum Leben erwachen. Tagsüber gehen die autonomen Fahrzeuge auf genau berechneten Strecken wie von Geisterhand bewegt ihrer Arbeit nach und sortieren alle Waren, die in Gitterboxen oder auf Europalette das Ladetor erreichen und per Förderband in die Halle gelangen, in die Hochregale ein. Nachts wird dann ausgelagert, was man am nächsten Tag benötigt. „Das System kann mit vier selbstfahrenden Fahrzeugen 35 Ein- und Auslagerungen pro Stunde vornehmen, das sind 280 pro Schicht“, so Produktionsvorstand Fischer.
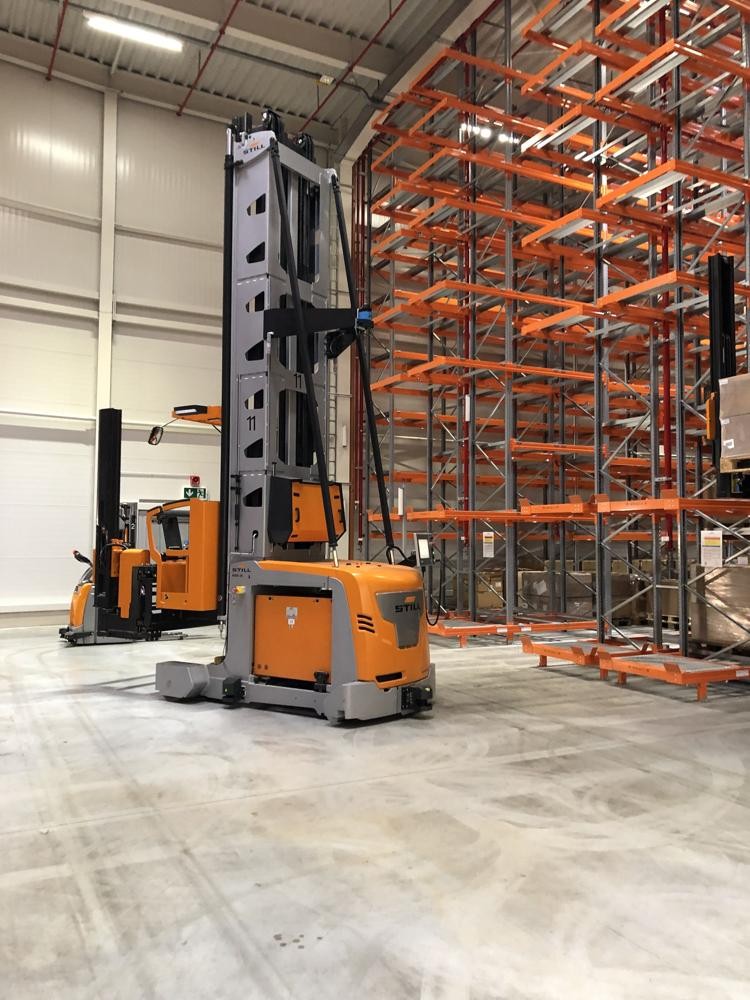
Fehler vermeiden und die Belegschaft entlasten
Angesichts der eindrucksvollen Zahlen drängt sich die Frage auf, wie man diese Mengen früher bewegt hat. „Auch wenn es für Außenstehende zunächst paradox klingt, sind wir froh, dass jetzt das System übernimmt. Es weiß zukünftig, welcher Artikel in welcher Menge in welchem Gebinde an welchem Platz liegt. Zudem ist es dank der aktuell leistungsstärksten Lagerverwaltungssoftware eWM on S4/HANA selbstoptimierend.“ Das automatisierte System ersetzt also keine Mitarbeitenden. Die Menschen können sich vielmehr anderen Aufgaben widmen, die für eine solche Software zu komplex wären. „Es ist günstiger, arbeitet ohne Beschädigungen und vermeidet Fehler“, fasst Dirk Fischer zusammen. Eine nachhaltige Lösung also, die aus der Not heraus entstanden ist. „Die Brandlast im alten Lager war zu hoch“, ergänzt Fischer. „Jetzt haben wir auch ein nachhaltiges Gebäude, das als Niedrigenergie-Halle nicht beheizt werden muss und über ein begrüntes Dach verfügt.“
Komplexe Aufgaben übernehmen zukünftig Spezialisten
Zur strategischen Bedeutung des Neubaus äußert sich der Vorstandsvorsitzende Hartmut Hagemann, der an die Ausführungen seiner Kollegen anknüpft und auf die zukünftige Ausrichtung des Unternehmens verweist. Die Zukunft der Möbelherstellung sei geprägt von einer zunehmenden Individualisierung. „Wir fertigen immer häufiger immer flexiblere Möbel und Raumlösungen auf Kundenwunsch an. Daher brauchen wir standardisierte und digitalisierte Lösungen für einfache Prozesse wie Ein- und Auslagerungen. Für Beratung, Projektplanung und alle komplexeren Aufgaben in der Produktion sind Köpfchen, Handarbeit und damit ein Team von Spezialistinnen und Spezialisten nötig. Dafür sind unsere Mitarbeitenden da, in deren Qualifizierung und Weiterbildung wir konsequent investieren.“